Pressure Gauge selection

How to Select the Right Pressure Gauge for Your Application

Selecting the correct pressure gauge for your industrial applications is essential for maintaining accurate pressure measurement, ensuring system safety, and achieving long-lasting performance. At IndSpare, we’re committed to helping you choose the perfect pressure gauge for your specific needs.
Key Considerations When Choosing a Pressure Gauge
To ensure you receive the right product, here are five key questions we typically ask:
1. What is the Scale Range?
The scale range defines the maximum pressure the gauge can measure. For optimal accuracy and gauge life, select a range that places your operating pressure near the midpoint of the gauge’s scale. At IndSpare, we offer gauges with scale ranges from 16 mbar up to 1,600 bar.
2. What Dial Size is Ideal?
Dial size impacts readability and space requirements.
- 63 mm (2.5”): Ideal for compact spaces or less critical readability needs.
- 100 mm (4”) or 160 mm (6”): Suitable for larger setups requiring easy readability.
3. Which Wetted Materials Are Needed?
The wetted parts are exposed to the process medium. You can choose:
- Specific wetted materials (e.g., stainless steel, Monel) for environments with corrosion risks.
- Let us know the process medium (e.g., gas, water, oil), and we’ll recommend suitable materials.
4. Liquid-Filled or Dry?
Liquid-filled gauges work best in environments with heavy vibrations, while dry gauges are suitable for stable applications.
5. What is the Connection Type?
The connection type ensures proper gauge attachment to your system:
- 1/4" NPT: Common for smaller dials (63 mm).
- 1/2" NPT: Common for larger dials (100 mm, 160 mm).
Additional Considerations for Specialized Applications
a) Is Calibration Required?
Calibration ensures accuracy and compliance with industry standards. We provide gauges with calibration certificates upon request.
b) What is the Pressure Type?
Most clients require gauge pressure, but some applications may need absolute or differential pressure gauges.
c) What Accuracy Level Do You Need?
Standard applications use 1.6% or 2.5% accuracy, while more precise needs may require 0.6% or 1.0% accuracy.
Popular Wika Gauge Models
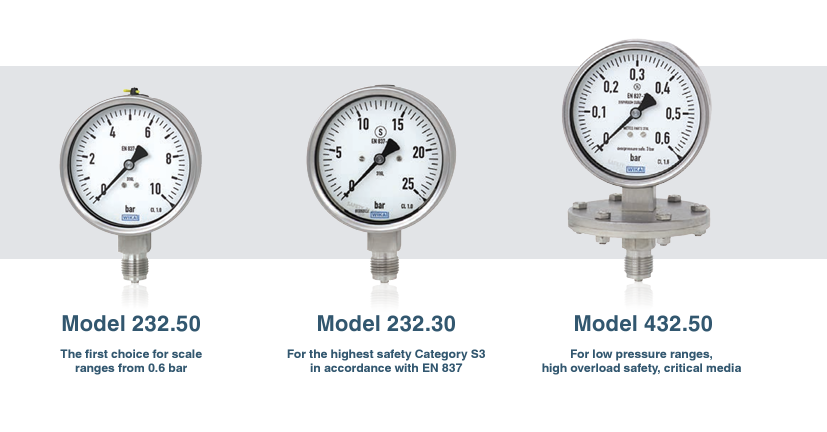
Here are some trusted Wika models for various applications:
- Model 232.50: For scale ranges from 0.6 bar.
- Model 232.30: High safety, Category S3 in line with EN 837.
- Model 432.50: Low-pressure ranges, high overload safety, critical media.
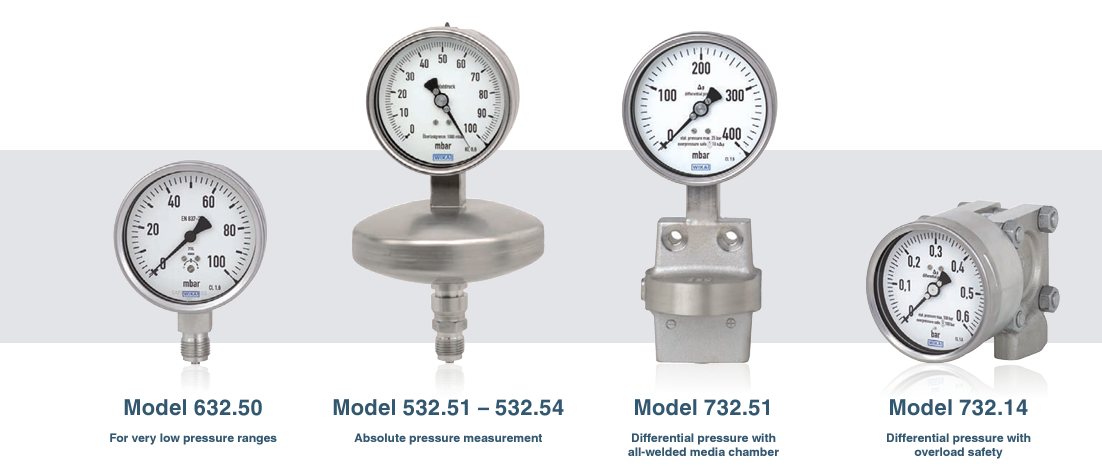
- Model 532.51: Ideal for absolute pressure applications.
- Model 632.50: Suited for very low-pressure ranges.
- Model 732.51: Differential pressure with a fully welded media chamber.
- Model 732.14: Differential pressure with overload safety.
Conclusion: Find the Right Gauge with IndSpare
At IndSpare, we are dedicated to helping you find the right gauge for your application. From high-pressure systems to precise readings, we’re here to support you every step of the way.
How to Select the Right Pressure Gauge for Your Application

Selecting the correct pressure gauge for your industrial applications is essential for maintaining accurate pressure measurement, ensuring system safety, and achieving long-lasting performance. At IndSpare, we’re committed to helping you choose the perfect pressure gauge for your specific needs.
Key Considerations When Choosing a Pressure Gauge
To ensure you receive the right product, here are five key questions we typically ask:
1. What is the Scale Range?
The scale range defines the maximum pressure the gauge can measure. For optimal accuracy and gauge life, select a range that places your operating pressure near the midpoint of the gauge’s scale. At IndSpare, we offer gauges with scale ranges from 16 mbar up to 1,600 bar.
2. What Dial Size is Ideal?
Dial size impacts readability and space requirements.
- 63 mm (2.5”): Ideal for compact spaces or less critical readability needs.
- 100 mm (4”) or 160 mm (6”): Suitable for larger setups requiring easy readability.
3. Which Wetted Materials Are Needed?
The wetted parts are exposed to the process medium. You can choose:
- Specific wetted materials (e.g., stainless steel, Monel) for environments with corrosion risks.
- Let us know the process medium (e.g., gas, water, oil), and we’ll recommend suitable materials.
4. Liquid-Filled or Dry?
Liquid-filled gauges work best in environments with heavy vibrations, while dry gauges are suitable for stable applications.
5. What is the Connection Type?
The connection type ensures proper gauge attachment to your system:
- 1/4" NPT: Common for smaller dials (63 mm).
- 1/2" NPT: Common for larger dials (100 mm, 160 mm).
Additional Considerations for Specialized Applications
a) Is Calibration Required?
Calibration ensures accuracy and compliance with industry standards. We provide gauges with calibration certificates upon request.
b) What is the Pressure Type?
Most clients require gauge pressure, but some applications may need absolute or differential pressure gauges.
c) What Accuracy Level Do You Need?
Standard applications use 1.6% or 2.5% accuracy, while more precise needs may require 0.6% or 1.0% accuracy.
Popular Wika Gauge Models
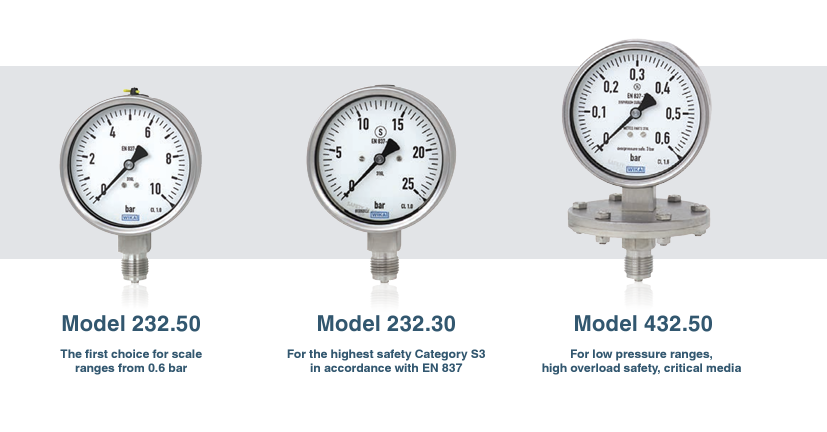
Here are some trusted Wika models for various applications:
- Model 232.50: For scale ranges from 0.6 bar.
- Model 232.30: High safety, Category S3 in line with EN 837.
- Model 432.50: Low-pressure ranges, high overload safety, critical media.
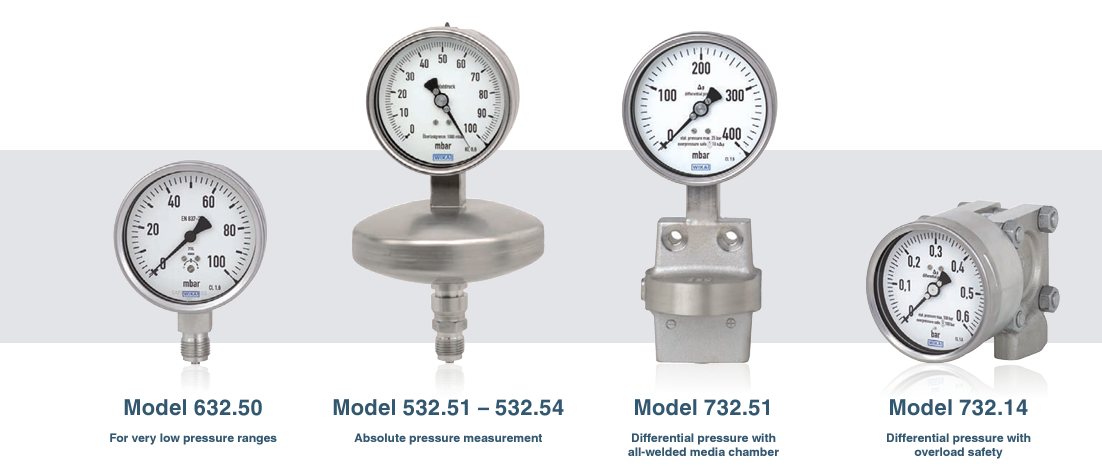
- Model 532.51: Ideal for absolute pressure applications.
- Model 632.50: Suited for very low-pressure ranges.
- Model 732.51: Differential pressure with a fully welded media chamber.
- Model 732.14: Differential pressure with overload safety.
Conclusion: Find the Right Gauge with IndSpare
At IndSpare, we are dedicated to helping you find the right gauge for your application. From high-pressure systems to precise readings, we’re here to support you every step of the way.